Setting the Bar High: The Role of Expectations in Critical Safety Processes
Many mature and aspiring health and safety programs set the bar high for the expected outcomes of critical processes, and for how those processes are built and executed. Essential safety processes are identified by OSHA in its seven “core elements” of effective safety and health programs — management leadership, worker participation, hazard identification and assessment, hazard prevention and control, education and training, evaluation and improvement and managing contractors and employees from temp agency. These processes are incorporated in the ISO international standard for occupational health and safety management systems (ISO 45001:2018) and the ANSI/ASSP Z10 occupational safety and health management standard.
Expectations run high for how fundamental safety processes are executed and for their outcomes because the stakes are high. Lives are at risk.
What does it mean when we set the bar high for expectations that mission critical processes will be robust and deliver positive outcomes? The Oxford Dictionary defines expectation as “a strong belief that something will happen or be the case in the future.” It is a belief, when applied to safety, that “something will happen” – a process will be properly executed and a positive outcome will be delivered. An expectation is not a rule. It is not a matter of confidence, excitement or suspense. Safety expectations are not predictions, forecasts, projections or calculations. Certainly, they are more than a hope. These are all synonyms for expectation, according to the Oxford English Dictionary.
The synonyms associated with expectation do have a place in safety work. Many workplaces have thick safety rulebooks. Leadership and the front line can be confident and excited about safety. And some safety practices can involve suspense, such as working at heights or in confined spaces. But these are not expectations. Safety predictors, indicators, forecasts, projections and calculations can be part of programs, but they are not beliefs.
Let’s examine high expectations for one essential process — hazard identification. First, we’ll look at expectations for how the hazard identification process is to be built and operated.
Hazard identification must:
- Be proactive and find hazards early before incidents occur
- Engage all levels of the organization — leadership and front line workers
- Permit individuals to slow down to see better and observe work environments in more detail
- Comprehensively and closely scrutinize the workplace to find and describe hazards both hidden and obvious
- Be executed without biases that create blind spots
- Emphasize critical thinking — curiosity, open-mindedness, analysis, interpretation, observation (the ability to notice and process details all around you) and problem-solving
- Analyze and assess hazard risks, interpret and describe what they mean in terms of the frequency and severity of exposures
- Communicate findings for controlling hazards prioritized by risk assessment.
Now let’s turn to numerous outcomes of this process. High expectations for what a well-executed hazard identification process will deliver means:
Incidents and near-misses are prevented because hazards have been identified, prioritized and mitigated
Tools and techniques are provided that improve how we see
Critical thinking and problem-solving is improved
Employees are more visually literate
Achieving these outcomes requires maturity and curiosity. Oxford defines maturity several ways, including having reached the most advanced stage in a process. Or the most advanced stage of safety. The use of Visual Literacy, for example, is a mark of an advanced hazard identification and assessment process.
The Need For Curiosity
Visual Literacy — the ability to understand and interpret hazards — will be limited if we don’t have an inquisitive, questioning mindset. Being curious is as important as being aware of the biases that can negatively affect Visual Literacy and hazard identification outcomes.
The Oxford dictionary defines curious as being eager to know or learn something. We must be eager to learn to see better, to describe and communicate hazard findings better, and to actively engage in hazard identification practices. Curious also means inquisitive, questioning, speculative and wondering. All are important qualities for advanced hazard recognition.
The Need for Visual Literacy
Delivering the best outcomes for hazard identification and assessment will not happen without visually literate employees. Visual Literacy is a powerful enabler to achieve high expectations because it improves how and what we see, how we interpret what we see, and taking corrective actions as a result.
Visual Literacy teaches us to slow down, look deeply and see things we may have previously missed. Being able to identify, interpret and mitigate hazards in the work environment is tremendously challenging today. Our senses, particularly our vision, are bombarded by a barrage of visual information. This is the visual age. We can’t expect the best outcome — to find and fix hazards, some hidden, some so obvious they are overlooked — if we are not trained to see better, to see without blinders or biases, and to apply critical thinking skills to describe, communicate and solve hazardous problems.
Critical thinkers are curious, eager to learn, skeptical, open-minded and unbiased. Evidence and reasoning are respected. Clarity and precision are emphasized. Adopting different points of view is essential. An organization cannot have the expectation of a safe day, which many mature organizations do, without a visually literate workforce that thinks critically.
Shifting Expectations
Operations with less developed and sophisticated safety and health programs often carry the expectation of a safe day resting in the hands of the individual workers. Workers are too often blamed when incidents and injuries occur, when hazards are not recognized or assessed properly.
More experienced organizations have expectations shaped by W. Edwards Deming’s thinking, as expressed in his book, “Out of Crisis.” Deming estimated that 94 percent of most troubles and most possibilities for improvement originated with systems — not people. He saw huge waste directed at blaming people for bad results. He wanted to focus improvements on the areas with the greatest possibility for results.
Organizations with advanced safety and health programs focus more on the systems and processes that people operate in. They see incidents or missed opportunities to identify and control hazards largely as organizational process failure rather than individual failure. The rationale: people will make mistakes, and it is the organization’s responsibility to install controls so when a mistake is made, the negative outcome is minimized if not prevented. Visual Literacy serves as an enabler to meet high expectations for hazard identification process execution and positive outcomes because it builds capacity for individuals to be keen observers, critical thinkers, problem solvers and communicators.
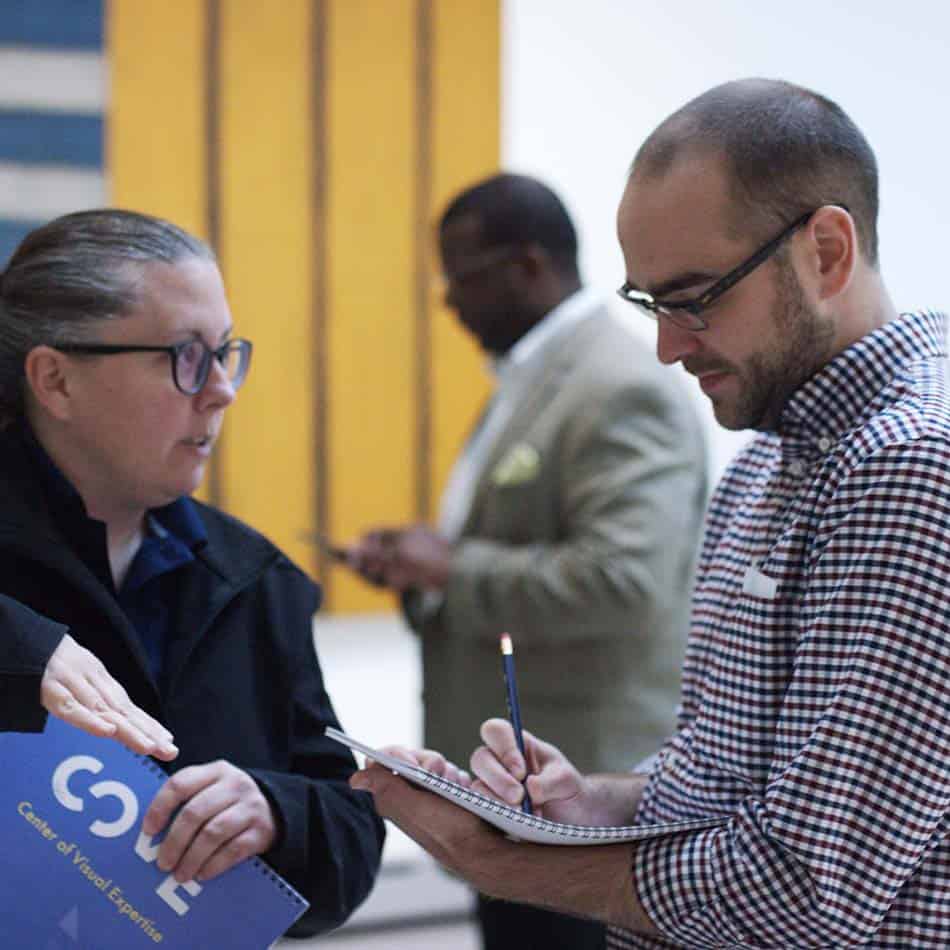
Developing a visually literate workforce means better observations, stronger communication, and more effective hazard mitigation—key elements in preventing incidents and creating a safer workplace.
Don’t leave safety to chance. Invest in Visual Literacy today!