The word “proactive” is tossed around in safety with little context. You’ve probably been instructed to “be more proactive” with your safety program. But often you’re not told how to be more proactive.
Ambiguity about the meaning of proactive leads to slivery platitudes about being proactive more than real-world practices. The fact is traditional safety approaches are often reactive, OSHA states in its Recommended Practices for Safety and Health Programs. That is, problems are confronted only after a worker is injured or becomes sick, a new standard or regulation requires compliance, or an outside inspection finds a violation that must be fixed.
Reactive safety and health programs are passive, unimaginative, and often irresponsible and fatalistic. External circumstances are blamed for injuries and fatalities instead of assuming responsibility and ownership for them. In reactive programs you hear excuses like:
“I told him to wear fall protection. I don’t know why he didn’t.”
“We didn’t expect that much rain when we dug those trenches. We didn’t have time to build the support.”
“That inspector has had it out for us for years!”
“Contractors are our biggest problem. They come on site and store chemicals any place convenient. They don’t pay attention when operating cranes and backhoes.”
Reactive programs can also exhibit what psychologists call “learned helplessness,” a fatalism. The most famous example: “Accidents will happen.” Other examples: “He was just unlucky; just wasn’t his day.” “Life isn’t fair. Bad things happen to good people.” “There was nothing I could do.” “He was disciplined three times. What else could we do?”
Not keeping pace
Signs point to traditional safety not keeping pace with the times. Former OSHA administrator Dr. David Michaels wrote a guest essay in the New York Times, “America’s Workplaces Are Still Too Dangerous.” “In recent years progress has slowed,” wrote Michaels. “Fatality rates plateaued more than a decade ago.” Michaels cited other problems: About 3.5 million workers are reported injured every year, but many injuries aren’t reported and the true number is higher; the maximum OSHA fine for a serious violation is “petty cash” to any large employer; and more businesses are abdicating responsibility for the people doing the work in their facilities by outsourcing to staffing agencies for gig workers, independent contractors and temps.
A troubling statistic: the overwhelming majority of international workers are not satisfied with workplace health and safety protections. According to a survey by Wakefield Research, 68 percent of workers across the world do not feel safe at work. Surveyed workers are most worried that building management won’t consistently enforce health and safety guidelines (42%), followed by worry that they won’t consistently invest in new technology to make working safer (30%).
Proactive safety principles
“Be proactive” is the first habit author Stephen Covey delves into in his classic book, “Seven Habits of Highly Effective People.” “Highly proactive people do not blame circumstances, conditions or conditioning… they work on things they can do something about…,” he writes. You can apply this behavior to workplace safety and health.
Safety experts Nick Stavropoulos, former COO of PG&E and National Grid U.S., and Emily Whitcomb, director of Work to Zero at the National Safety Council, offer seven principles of proactive safety:
- Speak up but also listen up and follow up
- Prioritize supporting your frontline workers
- Serious injuries and fatalities (SIFs) matter more than other injuries
- “Leave the Naughty List to Santa Claus”
- Performance and safety go hand-in-hand
- The right technology can make the difference
- Continuous improvement never stops
OSHA says its Recommended Practices for Safety and Health Programs “use a proactive approach to managing workplace safety and health. These recommended practices recognize that finding and fixing hazards before they cause injury or illness is a far more effective approach.”
The core elements of OSHA’s recommended practices are management leadership, worker participation, hazard identification and assessment, hazard prevention and control, education and training, program evaluation and improvement, and communication and coordination for host employers, contractors and staffing agencies. The seven proactive safety principles align with OSHA’s proactive recommended practices.
- Management leadership requires leaders to listen up and follow up.
- Work participation requires workers to speak up without being put on Santa’s “naughty list” and requires top management’s support.
- Hazard identification and assessment must focus on all hazards, and especially hazards causing serious injuries and fatalities.
- Program evaluation and improvement rests on understanding that the variability of everyday performance is the basis for safety.
- Hazard prevention and control requires continuous improvement that never stops.
- Education and training is paramount to supporting your frontline workers.
Foundational proactive safety
Finding and fixing hazards before incidents and injuries occur is foundational to proactive safety. It requires workers to be trained to see unsafe conditions at work; speak up – take responsibility to describe and communicate what they see; anticipate the potential of hazards to be precursors to SIFs through analysis and interpretation; collaborate and brainstorm on prevention and controls; and follow up to ensure hazards have been “fixed” –mitigated, abated, controlled.
Proactive safety webinar
Finding and fixing hazards requires Visual Literacy – the ability to see hazards in the workplace that have become so familiar we no longer see them, until the incident occurs. COVE: Center of Visual Expertise is presented a webinar on June 8th on “What Being Proactive In Safety Really Means,” The webinar explained how seeing the reality of our environment and work that our people do is key to taking the actions necessary in advance of an incident occurring. This is what proactive safety really means. The connection between Visual Literacy and hazard recognition, prevention through design, SIFs, and other common safety practices will be discussed. Be sure to watch the recording here.
Key webinar takeaways include:
- A traditional safety shortfall — being consumed with responding to incidents compromises our focus on prevention;
- Visual Literacy uses a high level of critical thinking to anticipate outcomes before they happen – true proactive safety;
- Simple tools are used to building the competency to see the reality of the world around us and take meaningful actions;
- Action is accelerated by communicating in a concise, objective manner.
The reality of today’s work environment – with everything from gigantic warehouses, robotics, artificial intelligence, unmanned transport, and digitized manufacturing facilities that use connected devices, machinery and production systems to collect and share data – is beyond the scope of traditional reactive safety. It is a complex, ever-changing reality that demands proactive thinking, behaviors and innovative practices.
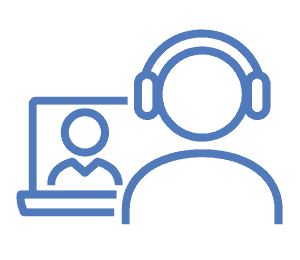
Webinar: Beyond The Buzzword:
What Being Proactive In Safety Really Means