To keep employees safe and maintain optimal safety performance, an organization must know how to successfully design, implement and improve upon its safety management processes and programs. Because the safety industry is ever changing, organizations must leave behind conventional safety approaches and the traditional mindset, and shift to fresh perspectives, which includes having a modern safety management system (SMS) in place.
In this article, we discuss why the antiquated schools of thought no longer work, define the modern safety management system and offer guidance for evolving your SMS. You will learn the connection between safety management systems and Visual Literacy, and how applying Visual Literacy methodology can elevate your safety strategy.
As long as your SMS is developed to reduce the risk of workplace incidents, injuries and fatalities; involves the entire organization; focuses on continuous improvement; and is proactive, then it matters less about what is actually included in your SMS. Each organization’s focus is different.
Safety training: If conducted effectively, safety training can develop safety awareness, regulatory compliance knowledge, knowledge of internal safety rules and procedures, abilities to find and fix hazards, to name a few. But the problem, according to Jennifer Lastra, CEO and co-founder 360 Immersive, LLC, is that most safety training is “superficial” filled with verbally-oriented lectures and instructions. Employee engagement and leadership involvement can be minimal, which is why Visual Literacy is the perfect methodology for safety training. It recognizes that we live and work in a visual world filled with imagery, and teaches how to understand those images and how to mentally organize them. Data management and document control: With many safety and health management systems comprised of scores of components and possibly hundreds of specific inputs or sub-elements, it is essential to collect and document accurate information on processes, products, potential hazards, safety and health practices and compliance. This can include documenting and updating injury data, annual reports, BBS observations, disciplinary actions and training activities. Visual Literacy training teaches employees how to accurately collect, assess and document safety and health-related data, including interpreting numbers, trends, patterns and analytics and providing concise descriptions and organization-wide messaging.
Why Conventional Approaches Are Not Good Enough
Many organizations have the best intentions when it comes to protecting their employees from harm, but unfortunately there can be a conventional mindset blocking the road to success or there are outdated systems and processes that are based on old-fashioned principles and have not been adapted to the current state of the organization. Factors such as having a remote workforce post-COVID, digital tools and systems, automated processes, or even a different focus on metrics beg for a new strategy and new approach to safety. Having conventional safety management system strategies still in place will not yield ideal outcomes let alone long-term success. Here are a few of those antiquated schools of thought that no longer work nor do they fulfill the purpose of great safety management. Heinrich’s Triangle The theory behind “Heinrich’s Pyramid” was that if you eliminated minor injuries and unsafe conditions, that the major breakdowns and catastrophes would be avoided. However, since some of the worst industrial accidents—the Challenger explosion, Deep Water Horizon disaster, the Texas City Refinery fire, etc.—happened and minor incidents and major catastrophes were not statistically linked, Heinrich’s theory isn’t as sound as once believed. BBS = blaming the worker One downfall of many behavioral-based safety processes, especially in their early years of use, is the common practice of focusing only on “negative behaviors.” This led to the perception that BBS was used to blame the workers. What these organizations need to realize is that safety isn’t about finding fault; it’s about collectively finding opportunities for learning and improvement. Many BBS processes have evolved to engage managers and supervisors in observations as well as include discussions of safe behaviors. Defaulting to administrative controls and PPE to solve problems Many times organizations turn to the bottom two controls in the Hierarchy of Controls to eliminate and control risk. Administrative controls and PPE, while they may be the easiest to use as a line of defense against hazards, they are the two least effective controls. Organizations need to consider using all the controls in risk mitigation and only resort to the two bottom controls if the controls (engineering controls, substitution, elimination) don’t eliminate the hazard or are in development.Developing a Modern Safety Management System
A safety management system is a strategic approach for managing safety risks in your organization. It aims to improve safety by developing processes or building on existing processes, demonstrating corporate due diligence and reinforcing overall safety culture. A SMS should not be confused with a series of checklists or a safety manual that ensures regulatory compliance. It’s not just a set of rules based on OSHA or HSE standards. It’s a collection of management elements that are identified and evaluated to develop and execute plans to improve your organization’s safety. SMS Applications and Areas of Consideration There are a number of frameworks and examples for developing a modern safety management system. In fact, the system build itself will depend on a few factors such as the size of an organization, documentation requirement, stakeholders and legal obligations. Despite there not being a system to model, the following general areas to consider including in your SMS:- Management leadership and commitment
- Hazard and risk Identification, evaluation and control
- Participation, awareness and communication
- Inspections
- Rules, procedures and written instruction
- Incident investigation processes
- Training and skill development
- Emergency response planning
- System administration and auditing
- Document management and control
As long as your SMS is developed to reduce the risk of workplace incidents, injuries and fatalities; involves the entire organization; focuses on continuous improvement; and is proactive, then it matters less about what is actually included in your SMS. Each organization’s focus is different.
Evolving Your SMS with Visual Literacy Training
From building leadership skills to conducting more effective incident investigations, Visual Literacy can help various areas of safety management systems. The following are just a few examples of how applying Visual Literacy benefits those areas: Leadership: The white paper explains that Visual Literacy helps leaders (managers, supervisors, safety professionals) see a work environment in its totality, so they can theoretically spot potential hazards and imagine what can happen due to those hazards. Additionally, having Visual Literacy skills helps leaders understand “how the worker sees (or doesn’t), why, and the implications of this for safety and health performance. Risk assessment and management (worksite analysis): We’ve previously discussed the role bias can play in risk management and incident investigations. It’s true that assessing risks will be flawed and judgements can be clouded when biases, assumptions and false perceptions surface. These are all to blame for being able to see as little as 10 percent of what you think you’re seeing. Hazards can easily be missed or overlooked, and risks can be prioritized incorrectly based on their probability, severity, and frequency. Visual Literacy helps you eliminate these biases and improve hazard identification and mitigation processes. Risk prevention and control: This element involves physical assessment of workplaces and human performance. Visual Literacy methodology can reveal gaps and hidden hazards in safety and health processes. The result is thorough, accurate and potential life-saving risk assessments. The white paper discusses how leveraging Visual Literacy tools and techniques improves inspections of:- Premises and housekeeping (lighting, ventilation, sanitation)
- Mechanical, electrical and personal safeguarding (machine guarding, lock-out/tag-out systems, personal protective equipment, exposure control)
- Fire protection and prevention (fire extinguishing equipment, storage of flammable and explosive material)
Safety training: If conducted effectively, safety training can develop safety awareness, regulatory compliance knowledge, knowledge of internal safety rules and procedures, abilities to find and fix hazards, to name a few. But the problem, according to Jennifer Lastra, CEO and co-founder 360 Immersive, LLC, is that most safety training is “superficial” filled with verbally-oriented lectures and instructions. Employee engagement and leadership involvement can be minimal, which is why Visual Literacy is the perfect methodology for safety training. It recognizes that we live and work in a visual world filled with imagery, and teaches how to understand those images and how to mentally organize them. Data management and document control: With many safety and health management systems comprised of scores of components and possibly hundreds of specific inputs or sub-elements, it is essential to collect and document accurate information on processes, products, potential hazards, safety and health practices and compliance. This can include documenting and updating injury data, annual reports, BBS observations, disciplinary actions and training activities. Visual Literacy training teaches employees how to accurately collect, assess and document safety and health-related data, including interpreting numbers, trends, patterns and analytics and providing concise descriptions and organization-wide messaging.
Taking Your SMS to the Next Level
Safety practices have shifted in the last few decades from conducting transactional activities that check the box to engaging processes that involve the entire organization in the effort to reduce incidents. Those organizations stuck in the conventional realm will not see the outcomes as those organizations who have modernized their approaches to safety management. It starts with evolution, in thought and in the tangible framework of a safety management system that will help an organization move forward. And with COVE’s guidance and Visual Literacy expertise, an organization can experience the growth and sustainability that ensures achieve optimal safety performance for the long-term.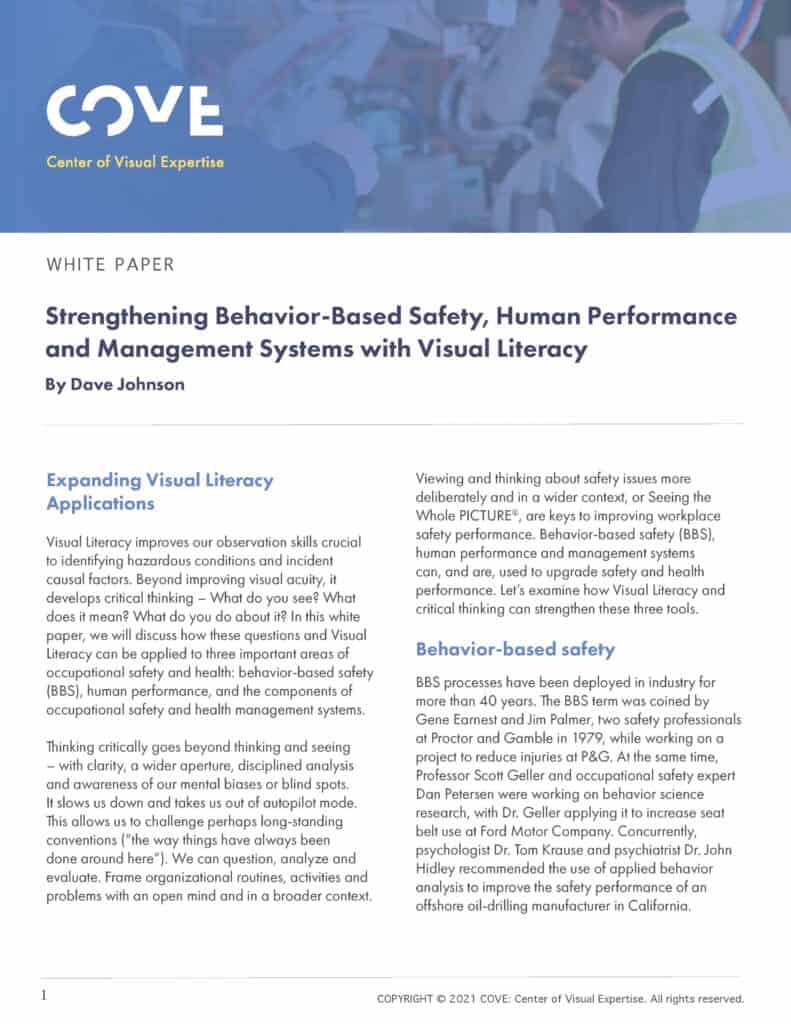
To further learn how Visual Literacy advances BBS, human performance and safety management systems, download the white paper “Strengthening Behavior-Based Safety, Human Performance and Management Systems with Visual Literacy.”