Why Risk Management is Crucial for Workplace Safety
To create a safer workplace and engage our people in continuous improvement in eliminating incidents, organizations must proactively manage risk. Without a roadmap, many can find it challenging to create a successful process. Without Visual Literacy skills that improve our ability to see the hazards in front of us, it is difficult to achieve total success.
In this article, we discuss the three building blocks of a risk management process. Applying these keys elements to risk reduction strategies can help organizations improve safety performance and ensure their workplace stays as a safe space. We also discuss how Visual Literacy enhances the execution of each building block.
The Risk Management Process
The risk management process is composed of identifying hazards, assessing their risk(s), and then working on a mitigation plan. Here’s an overview of each building block:
Step 1: Hazard Identification – The Foundation of Risk Management
The first step in the risk management process is hazard identification (also known as hazard recognition), which detects potential sources of harm or damage in the workplace. Organizations create an inventory of hazards to implement controls that will help ensure the safety of their workers and the community around them.
While hazard identifications can take on different forms and methods, the ISO 31000-2018 standard recommends that safety professionals and stakeholders examine a wide variety of factors, including, but not limited to:
- Tangible and intangible sources of risk
- Causes and events
- Consequences and their impact on goals and initiatives
- Knowledge limitations and information reliability
- Vulnerabilities
- Time-related factors
- Biases, assumptions, and beliefs of those involved
As an example of hazard identification, the American Society of Safety Professionals (ASSP) discusses HAZID, a hazard identification study that offers a qualitative, structured technique that helps identify risk (our next step in the risk management process). ASSP mentions that HAZID uses guide words and/or checklists to identify potential hazards, their causes, and consequences. In addition to its qualitative structure, HAZID can determine the potential severity of a particular hazard, as well as the likelihood of occurrence.
Visual Literacy provides the tools that help us see the reality of the world around us. Hazard identification is primarily a visual process. We look at the environment and tasks as they are done to identify the hazards that exist. We can’t fix what we don’t see.
Step 2: Risk Assessment – Understanding Potential Impact
After identifying hazards, the next building block involves conducting a risk assessment to find out whether a hazard poses a safety risk to employees and/or the community around them.
Much like hazard identification, a risk assessment can be deployed using a variety of methods, with familiar tools being the risk matrix, decision tree, failure modes and effects analysis (FMEA) and bowtie model. These may be different conceptually, but similarly look at the following criteria::
- Severity – What degree of harm could a risk have on worker safety, the environment, compliance, etc?
- Likelihood – How probable will the risk cause consequences?
- Frequency – How often are workers at risk?
- Risk levels – How are we measuring risk?
- Risk acceptability – What is the acceptable level of risk based on culture, industry, legal, and regulatory requirements?
- Risk treatment – What measures are required to achieve acceptable risk?
While conducting a risk assessment may take time to complete, it offers many benefits under the surface. For one, it helps set priorities for improvement, offering valuable insights into what risks should be addressed first and why. Second, the risk assessment process itself offers an opportunity to engage employees in safety initiatives and promotes those much-needed, leader-employee interactions. Everyone is working together to create a safe environment, while also collectively learning how to better identify and control risks in the workplace.
Visual Literacy advances our critical thinking competency and encourages us to image various outcomes that may be realized. By examining more thoughtfully the potential outcomes we can execute a risk assessment more completely and more accurately.
Step 3: Risk Mitigation – Taking Proactive Action
Identifying hazards and then assessing their risk potential brings needed clarity to what might harm the people near or around those hazards. After getting a clear picture of the hazard inventory and risk profile of those hazards, the next step is to develop and implement preventive and protective measures to mitigate future incidents.
But where does one start? Oftentimes the data and information collected can be too overwhelming that it can be challenging to develop a roadmap and navigate a path forward. And, like hazard identification and risk assessment, there is no standard protocol for how to perform risk mitigation. Fortunately, there are some key strategies and best practices available to help guide organizations.
One strategy is to consider applying the hierarchy of controls to the risk mitigation process. Now many organizations may already be doing this; however, we’ve seen that too often, these organizations turn to administrative controls and PPE as their primary line of defense against hazards. They should only be using these two controls if the controls higher in the hierarchy don’t eliminate the hazard or are in development. For maximum effectiveness, an organization must consider using all the controls in their risk mitigation strategy.
When using the hierarchy of controls, consider the following questions for each control:
- Elimination – Can I find safer ways to perform the task? If falling is the hazard, one solution can be storing stock at lower heights to avoid climbing ladders.
- Substitution – Can I use something less harmful? One example is using a less hazardous cleaner instead of something that is filled with harmful chemicals.
- Engineering controls – Are there any physical changes that can be made or equipment that can be used to prevent risk exposure? In the example of falling, guardrails can be installed as an engineering control.
- Administrative controls – Are there any safe work procedures that can be implemented? One example is prohibiting cell phone use while workers are driving/operating vehicles.
- PPE & clothing – Is there any personal equipment or clothing that can used to protect workers? While working with toxic chemicals may be necessary in some environments, protective eyewear, gloves and clothing will help reduce the risk.
As is the case with risk assessment, risk mitigation is enhanced by thinking critically about the potential solutions. Slowing down and examining creative and innovative solutions to the hazards identified can lead to breakthrough solutions. Visual Literacy provides tools that make slowing down productive and less uncomfortable in today’s fast-paced world.
Improving Risk Management at Your Organization
Many organizations may not be aware that they may need a structured risk management process. However, if injury and incident rates have plateaued or are increasing and/or if an organization desires to improve safety performance, a risk management process may be the best move. Once an organization performs risk management, it will have more visibility into all incidents before they happen and be able to fulfill proper risk reduction efforts to protect its workers and others from potential and future harm.
Visual Literacy and the associated tools provide value at each level of the process. Visual Literacy is all about what we see (hazard identification), what it means (risk assessment) and what we do (risk mitigation).
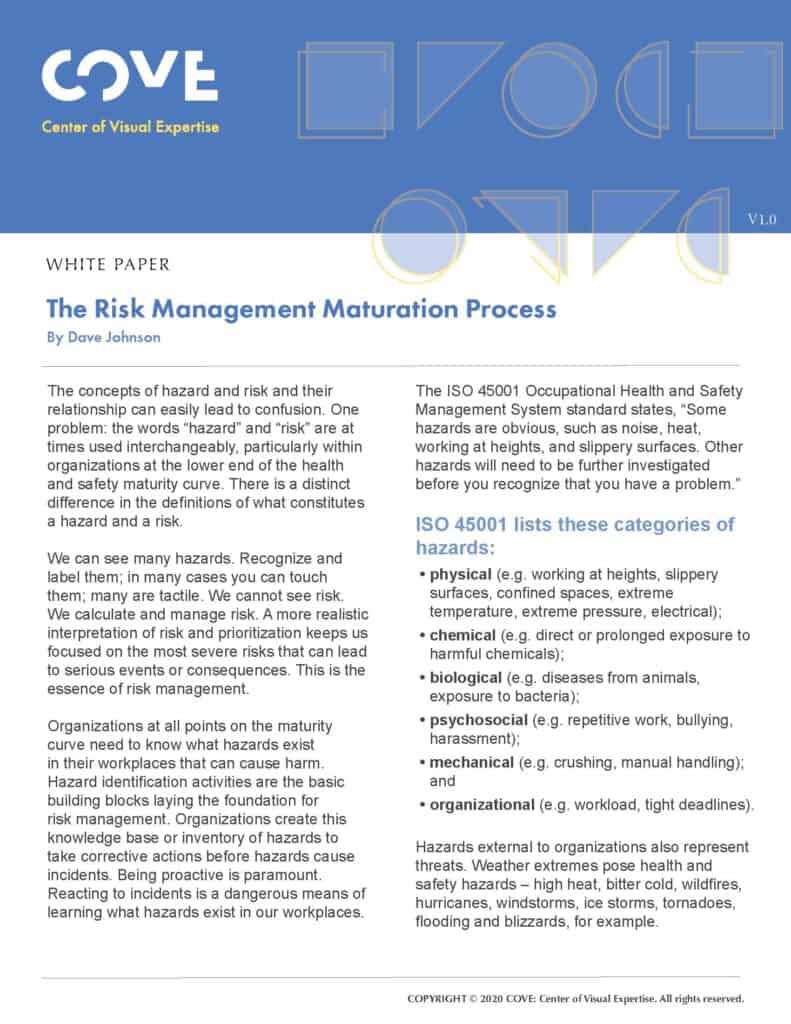
Ready to strengthen your risk management process? Explore how Visual Literacy training can empower your team to identify, assess, and mitigate risks more effectively. Download COVE’s white paper on The Risk Management Maturation Process.